- Joined
- Dec 29, 2007
- Messages
- 4,955
- Reaction score
- 3,142

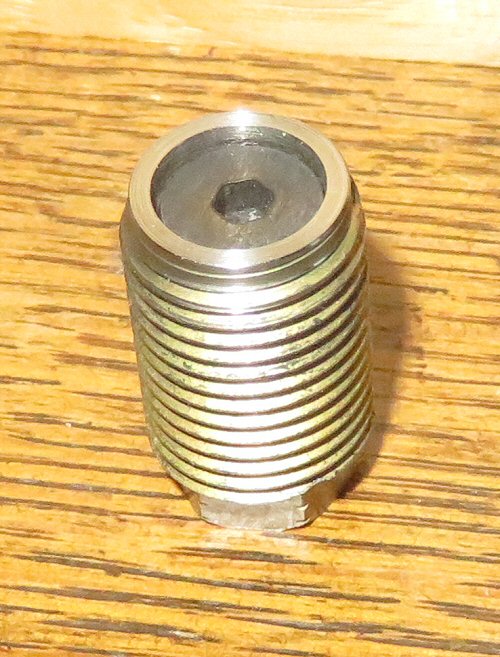
Breech plug is made from a 9/16" x 18 grade 8 bolt. Vent liner is made from a 10-32 holo-krome screw. Breech plug fits Woodman Arms Patriot rifle. Second such plug made here.
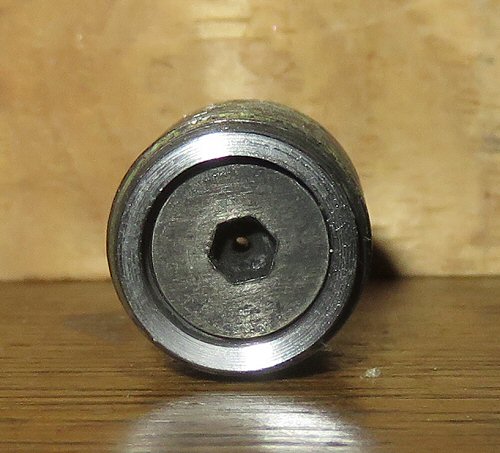
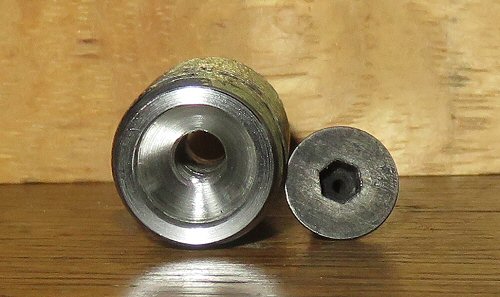
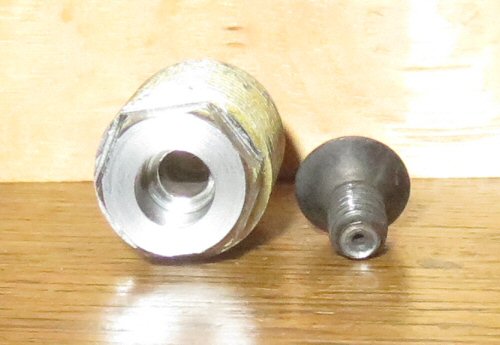
The screw/vent liner started out with a flash hole of 0.028", but now has grown to 0.033". The breech plug is long enough it has enough compression on primers to eliminate blow by.
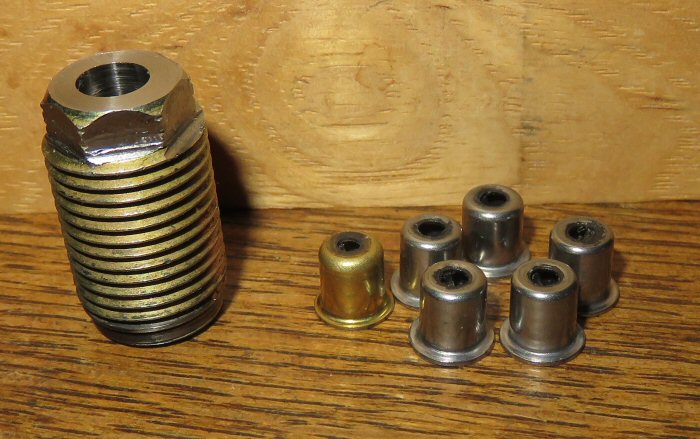